The secret of high efficiency of synchronous step-down DC/DC: we tell you by analyzing several products~
Time:2022-11-25
Views:1453
By Jeff Shepard
In various systems, including automobiles, industrial automation, telecommunications, computers, white goods and consumer electronics, the high bus voltage is reduced to a lower voltage, thus increasing the demand for power supply for IC and other loads. The challenge for designers is how to achieve this step-down conversion with the highest efficiency, minimum heat load, low cost and the smallest solution size possible.
Traditional asynchronous buck converter provides a potential low-cost solution, but its conversion efficiency is low and can not meet the needs of many electronic systems. Designers can use synchronous DC/DC converters and synchronous DC/DC controllers to develop compact and efficient solutions. This paper briefly introduces the performance requirements of electronic systems for efficient DC/DC conversion, and reviews the differences between asynchronous and synchronous DC/DC converters. Then, it introduces several synchronous DC/DC converter design schemes from Diodes, Inc, STMicroelectronics and ON Semiconductor, as well as evaluation boards and design guidelines. These solutions help to quickly start the development of efficient solutions.
Why do I need to synchronize the DC/DC converter?
All types of electronic systems require higher efficiency and higher complexity, which impels the power system architecture and power conversion topology to develop accordingly. As more and more independent voltage domains can support more and more functions, distributed power architecture (DPA) has been applied in more and more electronic systems. DPA does not use multiple isolated power supplies to drive different loads, but only includes an isolated AC/DC power supply used to generate relatively high distribution voltage, as well as a number of smaller step-down converters. The step-down converter is used to reduce the distribution voltage to a lower level according to the requirements of each load (Figure 1). The advantages of using multiple step-down converters lie in their small size, high efficiency and excellent performance.
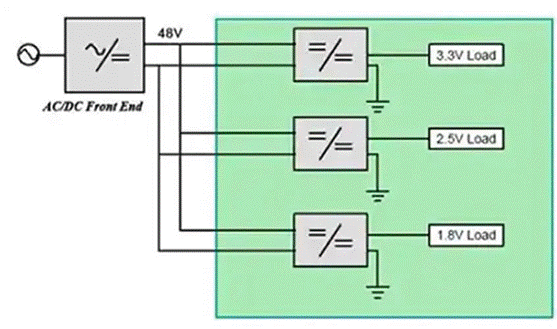
Figure 1 shows the distributed power architecture of the main isolated AC/DC power supply (front end) and multiple non isolated DC/DC converters that supply low-voltage loads. (Image source: Digi Key Electronics)
When choosing asynchronous or synchronous buck converter, there is a tradeoff between cost and efficiency. If the lowest cost solution is required, which can accept lower efficiency and higher thermal load at the same time, the asynchronous step-down solution may be the first choice. On the other hand, if the efficiency is given priority and the operation scheme with less heat is desired, the synchronous step-down converter with higher cost is usually a better choice.
Comparison of synchronous and asynchronous buck converters
A typical asynchronous step-down converter application is shown in Figure 2. LM2595 of ON Semiconductor is a monolithic integrated circuit, including main power switch and control circuit. The device uses internal compensation to minimize the number of external components and simplify the power supply design. The typical conversion efficiency is 81%, and the heat loss accounts for 19% of the power, while the typical conversion efficiency of the synchronous step-down scheme is about 90%, and the heat loss only accounts for 10% of the power. This means that the heat loss of the asynchronous buck converter is almost twice that of the synchronous buck converter. Therefore, the use of synchronous buck converter can reduce heating, thereby greatly simplifying the thermal management problems.
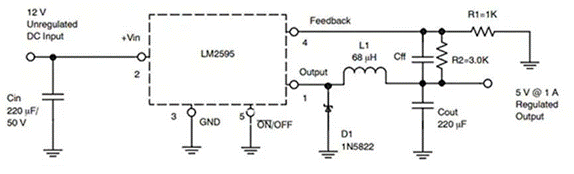
Figure 2: Typical asynchronous step-down converter applications, including output rectifiers (D1), output filters (L1 and Cout), and feedback networks (Cff, R1, and R2). (Image source: ON Semiconductor)
In synchronous buck converter, for example, ST1PS01 introduced by STMicroelectronics uses synchronous MOSFET rectification instead of output rectifier (Figure 3). Compared with the output rectifier in the asynchronous step-down converter, the synchronous MOSFET has a lower "on" resistance, which can reduce the loss and significantly improve the conversion efficiency. The synchronous MOSFET is an internal part of the IC and does not require an external rectifier diode.
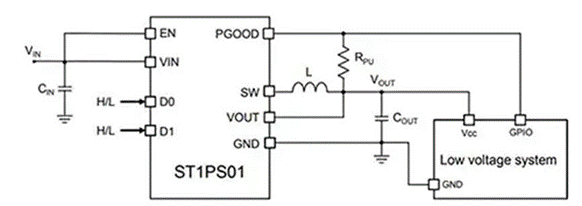
Figure 3: The synchronous step-down application circuit shows that the external output rectifier diode has been canceled. Output filtering and feedback components are still necessary. (Image source: STMicroelectronics)
Using synchronous buck converter can achieve higher efficiency and lower heat load, but it has a cost. Since only one power switch MOSFET and one rectifier diode are included, the possibility of cross conduction or "penetration" need not be considered, and synchronous FET is not required for control, the asynchronous step-down converter controller is much simpler and smaller. The synchronous step-down topology requires more complex drivers and anti cross conduction circuits to control the two switches (Figure 4). To ensure that the two MOSFETs do not conduct at the same time and have a direct short circuit, more complex circuits are required, which in turn requires larger and more expensive ICs.
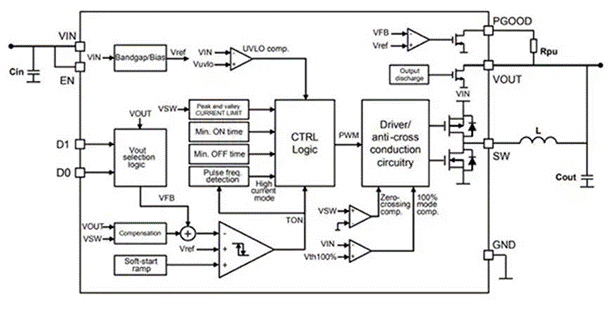
Figure 4: The synchronous buck converter IC block diagram shows two integrated MOSFETs (pins marked with "SW" next to them) and the added driver/anti cross conduction circuit. (Image source: STMicroelectronics)
Although PWM controlled synchronous buck converter has higher efficiency under medium or full load conditions, asynchronous buck converter usually has higher conversion efficiency under light load conditions. However, this situation is gradually decreasing, because the latest implementation of synchronous buck converter includes multiple operating modes, allowing designers to optimize low load efficiency.
Synchronous step-down for 5V and 12V distribution
Diodes, Inc. introduced the AP62600 device for designers who use 5V and 12V power supplies for power distribution in consumer products and white goods. This is a 6 amp (A) synchronous step-down converter with an input range of 4.5 to 18 volts. The device integrates a 36 milliohm (m Ω) high voltage side power MOSFET and a 14 m Ω low voltage side power MOSFET to achieve high efficiency buck DC/DC conversion. Since the AP62600 uses a constant on time (COT) control mode, it requires only a few external components. The device also has the characteristics of fast transient response, easy loop stability and low output voltage ripple. The AP62600 is optimized for electromagnetic interference (EMI) suppression. The device uses a proprietary gate driver scheme to prevent transient oscillation of switch nodes without sacrificing MOSFET on and off time, thus reducing high-frequency radiated EMI noise caused by MOSFET switches. The device is packaged with V-QFN2030-12 (Type A). It is equipped with a "good power" indicator light to remind users of possible failures. The programmable soft start mode can control the surge current when powered on, enabling designers to achieve power sequencing when using multiple AP62600 to power large integrated devices, such as field programmable gate array (FPGA), specific application IC (ASIC), digital signal processor (DSP) and microprocessor unit (MPU). The AP62600 provides three operation modes for designers to choose to meet the specific needs of personalized applications (Figure 5). High efficiency of all loads can be achieved through pulse frequency modulation (PFM) operation. Other available modes include Pulse Width Modulation (PWM) for optimum ripple performance and Ultrasonic Mode (USM) for avoiding audible noise at light loads.
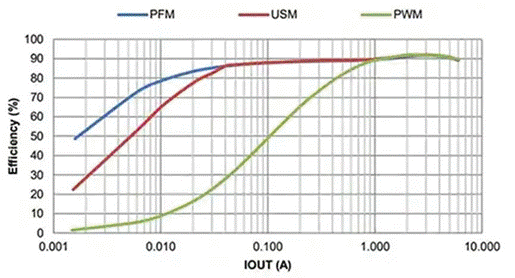
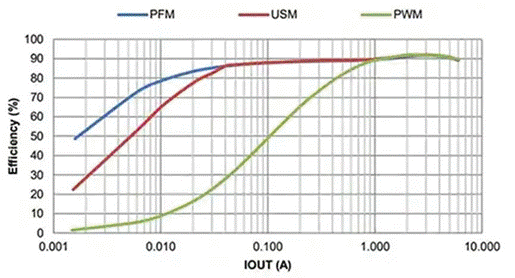
Figure 5: AP62,600 provides designers with three working modes to meet the requirements of personalized applications: PFM, USM and PWM. (Image source: Diodes, Inc.)
To help designers get started with AP62600, Diodes, Inc. also provides AP62600SJ-EVM evaluation board (Figure 6). The AP62600SJ-EVM has a simple layout and can access corresponding signals through test points.
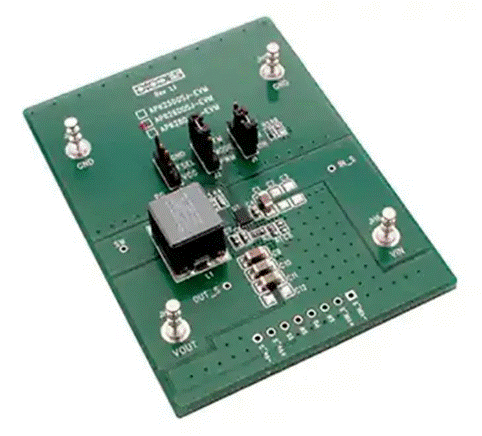
Figure 6: The AP62600SJ-EVM evaluation board provides a simple and convenient evaluation environment for the AP62600. (Image source: Digi Key Electronics)
Synchronous step-down of 24 volt bus
STMicroelectronics L6983CQTR has an input range of 3.5 to 38 volts and an output current of up to 3A. Designers can use the L6983 for a wide range of applications, including 24 volt industrial power systems, 24 volt battery powered devices, distributed smart nodes, sensors, and always on and low-noise applications. The L6983 is based on a peak current mode architecture with internal compensation and is packaged with 3mm x 3mm QFN16, thus minimizing design complexity and size. The L6983 is available in Low Consumption Mode (LCM) and Low Noise Mode (LNM) versions. LCM maximizes light load efficiency by controlling output voltage ripple, making the device suitable for battery powered applications. LNM mode can keep the switching frequency constant and minimize the output voltage ripple to achieve light load operation, thus meeting the requirements of low noise applications. L6983 allows switching frequency selection in the range of 200 kHz to 2.3 MHz, and can select spread spectrum to improve EMC. STMicroelectronics provides the STEVAL-ISA209V1 evaluation board to help designers explore the functions of the L6983 synchronous monolithic step-down regulator and quickly start the design.
Synchronous buck controller for computing and telecom design
NCP1034DR2G of ON Semiconductor is a high-voltage PWM controller for high-performance synchronous buck DC/DC applications with input voltages up to 100 V. The device is designed for 48V non isolated power conversion in embedded telecommunications, network and computing applications. NCP1034 drives a pair of external N-channel MOSFETs, as shown in Figure 7.
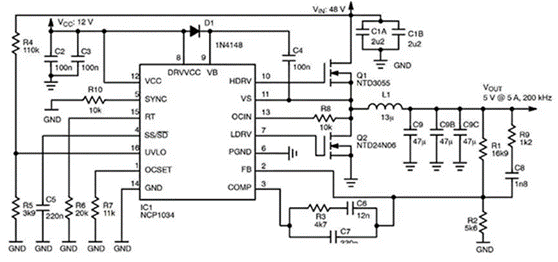
Figure 7: The typical application circuit of NCP1036 synchronous step-down controller IC shows the MOSFETs on the high side and low side (Q1 and Q2 respectively). (Image source: ON Semiconductor)
The NCP1036 has a programmable switching frequency range of 25kHz to 500kHz and a synchronization pin for externally controlling the switching frequency. By providing these two frequency control modes, the designer can select the best value for each specific application and make multiple NCP1034 controllers work synchronously. The device also includes user programmable undervoltage lockout and burp current limiting protection. For low voltage designs, an internal fine tuned 1.25 volt reference can be used to achieve more accurate output voltage regulation. It includes four undervoltage lockout circuits to protect equipment and systems. Three circuits are designed to protect specific functions; Two for protection of external high-voltage side and low-voltage side drivers; One is used to protect the IC from premature startup before the VCC falls below the set threshold. The designer can program the fourth undervoltage lockout circuit by using an external resistance divider: as long as the VCC is below the threshold set by the user, the controller will remain disconnected. To help designers start using NCP1034, ON Semiconductor also provides the NCP1034BCK5VGEVB evaluation board (Figure 8). The design of the evaluation board provides several options to meet various system requirements. There is a linear regulator to supply power to the IC; To this end, designers can determine whether to use Zener diodes or high-voltage transistors by selecting appropriate resistors. Designers can also choose the second (voltage mode) compensation or the third (current mode) compensation, ceramic or electrolytic output capacitors, and various input capacitance values. It is equipped with two needle bases: one is used to conveniently connect the external synchronous pulse source, so that the board can be directly connected to another NCP1034 demonstration board; The other pin holder is connected to the SS/SD pin, and the controller can be turned off by connecting the ground.
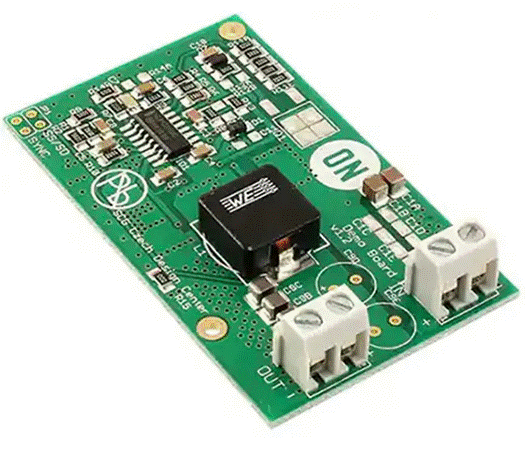
Figure 8: The NCP1034BCK5VGEVB evaluation board provides multiple options to help designers quickly start new designs. (Image source: Digi Key Electronics)
epilogue
In automotive, industrial automation, telecommunications, computers, white goods, consumer electronics and other systems, it is increasingly necessary to reduce the high bus voltage to a lower voltage in order to supply power for IC and other loads.
As shown in the figure, designers can turn their attention to synchronous step-down power converters to achieve step-down conversion with the highest efficiency, minimum heat load, low cost and the smallest solution size.
Disclaimer: This article is transferred from other platforms and does not represent the views and positions of this site. If there is any infringement or objection, please contact us to delete it. thank you! |