External and Integrated MOSFET Architecture in Brushless Direct Current BLDC Motor Systems
Time:2023-09-18
Views:600
If you are not familiar with motor drive systems and want to know the meaning of external MOSFET architecture and integrated MOSFET architecture, then you have found the required FAQ page! Even experienced motor system designers often do not know which MOSFET architecture to choose for a given system. In this FAQ, I will introduce you to two architectures of power MOSFETs. Although this FAQ involves three-phase BLDC systems, the concept can be easily extended to different types of DC motor systems, such as single-phase BLDC motors, brushless DC motors, or stepper motors.
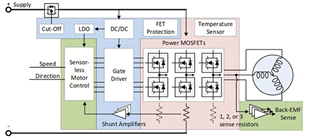
Figure 1: Typical Sensorless BLDC Motor System
Figure 1 shows a typical sensorless BLDC motor system. The components highlighted in blue are usually part of the gate driver integrated circuit (IC), where the power MOSFET is located outside the IC on the circuit board. When the gate driver IC also includes components highlighted in red, the IC is referred to as a motor driver or integrated FET driver. The components highlighted in green are part of the motor controller. We will focus on discussing gate driver and motor driver architectures.
Gate driver architecture: By selecting different MOSFETs to expand power levels, an external MOSFET based architecture allows system designers to flexibly use the same driver and control design for various applications. Usually, MOSFETs with higher rated currents have larger packaging dimensions to adapt to the lower R (ON) of MOSFETs and provide better thermal performance. System designers can choose different MOSFETs based on system performance requirements and optimize circuit board sizes accordingly. Due to the fact that MOSFETs can be placed in distant locations on circuit boards, gate driver architectures typically provide better thermal performance. One drawback of the gate driver based architecture is that the circuit board design is complex, due to the placement of six MOSFETs on the circuit board (for three-phase BLDC systems). In order to achieve system performance goals such as lower EMI and noise, system designers also need to consider the MOSFET position in the gate driver IC. Due to the large number of components on the circuit board, the gate driver system is much larger than motor driver solutions of the same power and voltage level. An example of a gate driver board is the DRV8304 EVM, which is a 40V BLDC system designed to provide 15A current. The size of the EVM circuit board is 61mm x 56mm (3233 square millimeters). Compared to gate driver ICs, six MOSFETs occupy 2.5 times the area on the circuit board!
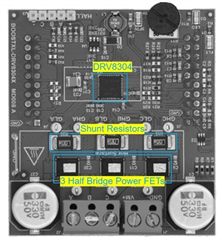
Figure 2: DRV8304 EVM Circuit Board
Motor driver architecture: An architecture based on integrated MOSFETs can simplify system board design, and the solution size is much smaller compared to gate driver systems. The motor driver system can also shorten the design cycle, as system designers do not need to consider optimizing MOSFET gate drive technology to reduce EMI, noise, or thermal performance. The motor driver IC developers have already considered these issues when designing the IC! A typical motor driver IC can provide motor currents of 1A to 10A. Due to the integration of six MOSFETs in a small package (usually less than 10x10mm), the thermal performance of motor driver ICs is often poor. Designers need to choose motor driver ICs with lower FET R (ON) to meet their system thermal performance requirements. Based on experience, approximately at power levels above 70-80W, system designers began to switch from a motor driver based architecture to a gate driver based architecture in order to achieve better thermal and power transmission performance. TI‘s new BLDC motor driver DRV8316 integrates six 50m Ω MOSFETs, suitable for three-phase BLDC systems. The size of the DRV8316 EVM board is 19.8mm x 16mm (317 square millimeters), and it has the same motor voltage level as the DRV8304 board, which is 10 times larger in size!
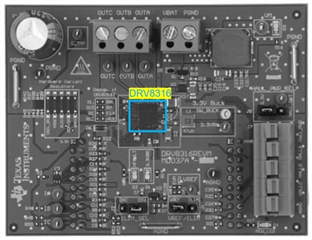
Figure 3: DRV8316 EVM circuit board
Overall, systems based on gate driver architecture are flexible, but larger in size and complex in design. The system based on the motor driver architecture is simple and compact, which can shorten the design cycle, but may not meet all the thermal performance requirements of the system. In low-power applications, it is best to use a motor driver architecture, especially the all-new DRV8316, which can provide up to 70W of power in a packaging size of only 35 square millimeters.
Disclaimer: This article is transferred from other platforms and does not represent the views and positions of this site. If there is any infringement or objection, please contact us to delete it. thank you! |