There are many challenges in power supply design, dealing with high current can solve worries
Time:2023-09-28
Views:568
In the opening remarks, it was mentioned that the most important factor in power supply design is the current, and the magnitude of the current determines the difficulty of power supply design. So, has the current of the power supply only started to increase in recent years? Didn‘t there be a high current power supply design in the early years? The answer is certainly no! So what are the differences between the high current design of power supplies in recent years and before?
My summary is: one is high voltage high current, and the other is low voltage high current.
Design Difficulties of High Voltage and High Current Power Supplies
Ten or twenty years ago, the era was not without high current power supply designs, but rather the vast majority of high current single boards, which were either power boards or backplanes. For ordinary functional boards or board type single boards, the IO voltage of the chip is mostly 3.3V or 5V, and the current is usually not too large, mostly below 10A, usually a few amperes. On the other hand, when the power board or backplane has a high current, the voltage is also relatively high, above 12V, 36V, and 48V. So I summarized it as the design challenge of high voltage and high current.
To cope with high voltage, we need to pay attention to safety regulations and various safety distances, including air gaps, creepage distances, etc. Concerned about safety related design requirements such as flame retardancy and insulation. This is another large category, and I won‘t go into detail here. If you are interested, you can look for relevant information. Yibo Technology also has relevant experts responsible for safety regulations design.
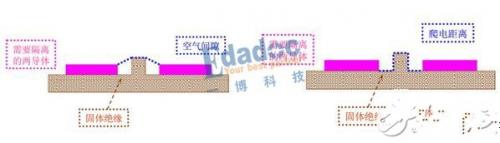
This type of [size=1em] PCB design can also have high currents, ranging from tens of amperes to hundreds of amperes. But this type of board has another characteristic, which is that there are basically no functional circuits on it, that is, your CPU, DDR particles, large-scale FPGA, etc. These circuits are not implemented on the power board. A power board is a power board that contains components that perform power functions, such as large inductors, capacitors, resistors, diodes... In a word, the components are all very large.
This type of design addresses the design challenges of high currents, and the solutions are also simple and crude. Try to route the wires as thick as possible and use copper foil as wide as possible. If it still cannot meet the requirements, use thick copper. If it cannot meet the requirements, it will be 4oz. If it cannot meet the requirements, it will be 6oz, 10oz, or even 12oz. We have displayed a thick copper plate in various seminars, which is a 12oz copper foil thickness design. A small piece of board looks very thick and heavy. Our craft expert Dong Ge‘s introduction is: it is essential for self-defense when traveling at home^-^
The traditional design rules for dealing with the high current of such power boards are also simple and rough over design. So the current carrying answer in people‘s minds is often very conservative, such as 1 ampere current, which requires approximately 40 mils of line width; A 10~12mil through hole can only carry 0.5 amperes of current, and I even heard someone answer that a 12mil through hole carries 0.2 amperes of current. I was thinking at the time, if your design was for a 20 ampere current, how many vias would you need to punch?
So we come to another challenge in power supply design
Design difficulties of low-voltage high current power supply
In fact, high pressure and low pressure are not the main dividing points between these two types of problems. The main difference I really want to say is that traditional functional circuits, such as CPUs, DSPs, large-scale FPGAs, and cores, often have currents of tens of amperes, and the current of IO power supplies is becoming increasingly high. The trend of power supply design is shown in the following figure:
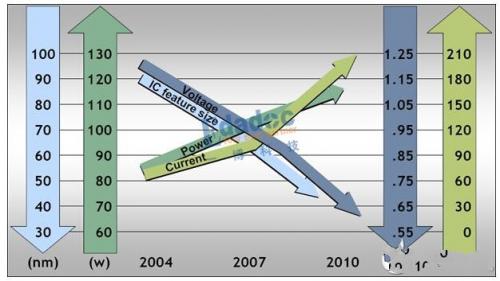
At this time, the high current makes it impossible to use thick copper plates because there are still a large number of signal lines on the plate, with a width of only a few mils. The area of copper skin is sometimes limited to "layer" resources and a large number of dense pores, and the limited area of copper skin is also difficult to infinitely increase.
How can we address the challenges of high current design with dense vias, limited board area, and number of layers, as shown in the following diagram? How do we calculate the necessary current carrying channels (including the width of the copper sheet and the number of through-holes)?
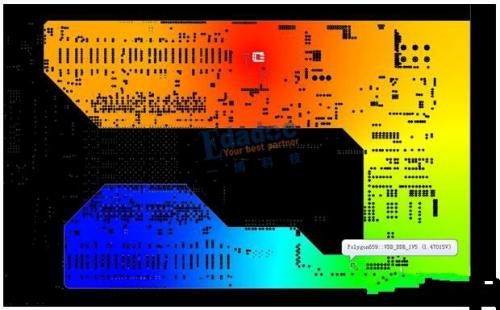
And low voltage can also bring additional design difficulties. As mentioned in the previous article, the higher the current, the larger the corresponding △ I, and under a certain inductance, the greater the induced △ V. The lower voltage, the smaller the design margin, and the greater the difficulty of design.
As shown in the figure below, the issues of DC and AC together constitute the problem of power supply design.
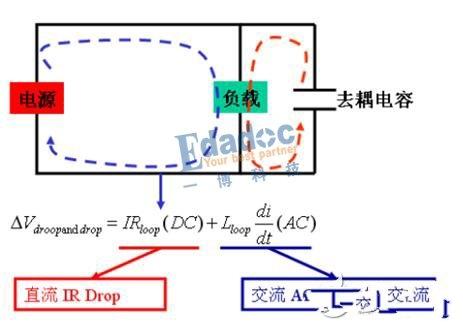
A power supply that meets a design margin of 5% must be considered together with AC and DC.
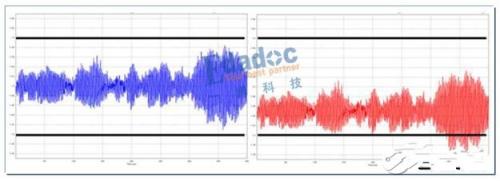
Disclaimer: This article is transferred from other platforms and does not represent the views and positions of this site. If there is any infringement or objection, please contact us to delete it. thank you! |