Mainstream motor control chip solutions, 2022 motor control drive chip inventory
Time:2024-03-08
Views:181
In recent years, high-efficiency motors have been highly valued by the industry, and many chip manufacturers have also begun to turn their attention to the motor drive and control market. Due to the high efficiency, low noise and other advantages of BLDC/PMSM motors, more and more industrial systems, home appliances, PC and other systems are using more energy-efficient BLDC/PMSM motors. However, these types of motors require complex hardware and optimized software design to improve their performance. In order to facilitate designers to quickly and efficiently design motor control and drive solutions that meet their needs, different chip manufacturers are also increasing their investment and designing many new motor control and drive chip products. Today, let‘s take a look at which manufacturers have launched new products this year.
In recent years, ST has mainly been promoting its STSPIN32 series products. Recently, ST has launched two reference designs based on STSPIN32 motor control SiP to help engineers simplify the development of industrial or household compressor motor drivers. Among them, the target application of STEVAL-CTM011V1 is a general-purpose industrial compressor with a maximum output of 250W, while STEVAL-CTM012V1 complies with strict household energy efficiency regulations. These two plug and play reference designs are easy to integrate with the main control system, start the motor, and allow customers to fine tune the settings for optimal performance. The average energy efficiency of both reference designs is greater than 96.5%.
The MOTIX product series is a power bridge series designed for various 100mA to 70A automotive and industrial applications, equipped with various functional sets. For example, high-power DC motor bridges can provide flexible and scalable solutions for motor drive from DC 2A to peak current 70A, with different functional options that can be used in various application fields. Intelligent power motor bridges are composed of various bridges specifically designed for automotive and industrial applications.
TI: 19 motor drivers have been launched in the past 12 months
TI is an old player in the field of motor drive chips, and its motor drive products include gate drivers, H-bridge drivers, brushed motor drivers, and BLDC motor drivers. There are also a wide variety of product types and models, and in the past 12 months, 19 new motor drive products have been launched.
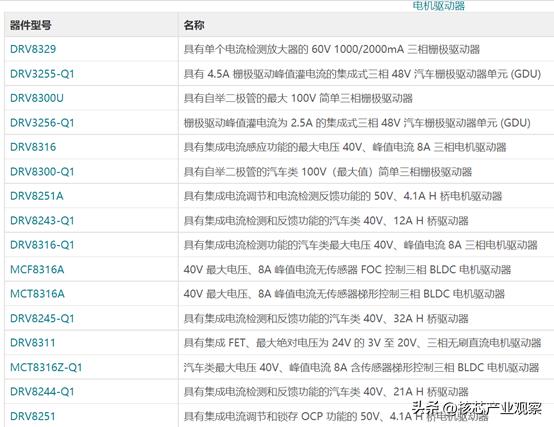
Image: TI‘s new motor driver products released in the past 12 months (source: TI‘s official website)
According to TI‘s press release, the 70W BLDC motor drivers MCT8316A and MCF8316A launched last year can be used for trapezoidal and field oriented control (FOC) without programming or sensors, allowing engineers to start the BLDC motor within 10 minutes. They can be used in various industrial systems, household appliances, respiratory machines, and medical equipment such as continuous positive airway pressure ventilation machines.
It is reported that the MCF8316A and MCT8316A brushless DC motor drivers include a series of unique commutation control algorithms that do not require the development, maintenance, and verification of motor control software, thereby reducing several weeks of design time. These algorithms and highly integrated features can enable the motor driver to better manage key functions such as motor fault detection, while implementing protection mechanisms to improve system reliability. These motor drivers integrate sensorless technology to determine rotor position, eliminating the need for external Hall sensors, which can reduce system costs and improve reliability.
The MCT8316A sensorless trapezoidal control motor driver can achieve a maximum motor frequency of 3.5kHz and can reduce BLDC motor noise through different trapezoidal control techniques; MCF8316A, on the other hand, includes a patented precision automatic dead time compensation technology. This technology can compensate for current distortion and greatly optimize the acoustic performance of the motor.
In addition, MCF8316A and MCT8316A can reduce the board space for designers by up to 70% and lower the total cost of the motor system. These devices integrate three gate drivers and six high and low side MOSFETs, each with a conduction resistance of 50m Ω. This allows these two devices to provide up to 70W of power and 8A of peak current in 12V and 24V systems. These motor drivers also integrate components such as low voltage drop (LDO) regulators, DC/DC drop regulators, and current detection amplifiers, eliminating up to 18 discrete components.
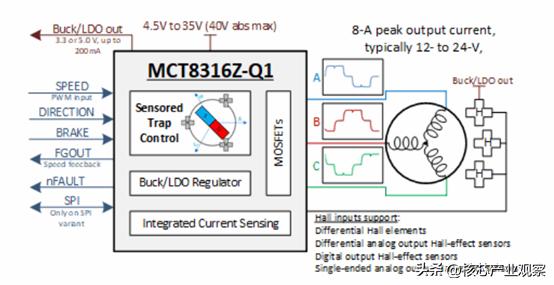
Two months later, TI launched the MCT8316Z on the basis of two BLDC drivers, MCF8316A and MCT8316A, providing customers driving 12V to 24V DC motors with a single chip, code free, and sensor ladder option. This chip integrates a three-phase BLDC motor driver controlled by a trapezoidal sensor, with an absolute maximum operating voltage of 40V and a maximum output current of 8A. MCT8316Z uses a Hall sensor with 120 ° commutation, and supports analog or digital Hall inputs. This device supports PWM frequencies up to 200kHz, and PWM also supports synchronous and asynchronous modulation. In addition, the device also has a vehicle grade version.
ST: Continue to launch highly integrated motor control chips
ST has also invested a lot in motor drive products in recent years, as can be seen from its industrial summit. In recent years, the ST industrial summit will have a separate motor control sub forum. From its official website, it can be seen that ST has four major categories of products in motor drivers: MOSFET and IGBT drivers, brushless DC motor drivers, brushless DC motor drivers, and stepper motor drivers.
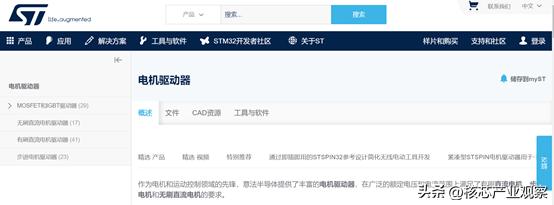
According to its press release, the core components of these two reference designs are both ST‘s STSPIN32F0601Q motor control SiP. This SiP integrates the STM32F031 Arm Cortex-M0 microcontroller and a highly robust 600V three-phase gate driver. The microcontroller supports customizing motor control algorithms based on the specific requirements of the terminal application, and the gate driver is used to control the inverter switching transistor. The supporting firmware includes an efficient sensorless vector control (FOC) algorithm. This SiP is a compact, high thermal efficiency square flat lead-free (QFN) package that meets the strict requirements of safety and reliability for creepage distance.
In terms of automotive grade motor controllers, ST also launched L99DZ200G in 2022, which includes two H-bridge gate drivers, a gate driver used to drive external MOSFET power transistors to control mirror heating, a control unit and high side driver used to control automatic anti glare mirror dimming, and five LED high side drivers, three of which can operate in constant current mode, Power the lighting module with high input capacitance, and two other high edge drivers are used to control ordinary LED lighting.
Through two H-bridge drivers, L99DZ200G can simultaneously control two spindle motors and drive an additional tightening motor to close the electric tailgate or trunk. Both drivers can operate in generator mode, and when overvoltage is detected in the power rail, both low side MOSFET switches can be activated simultaneously to protect the controller.
Engineers can achieve front window, rearview mirror, lighting, and rear window lifting functions through a single L99DZ200G chip.
Infineon: The integration of automotive grade motor drive chips is increasing
Infineon‘s motor control solutions can be used in automotive, consumer, and industrial applications, mainly in the iMOTION and MOTIX sub series products. The iMOTION series is mainly used for industrial and consumer motor control applications, and this product series provides multi-level hardware and software integration. The multi-level hardware integration refers to the broad span from independent motor controllers to a complete inverter system integrated on SmartIPM. The multi-level integration of software means that Infineon provides both a complete turnkey solution and modules for developers to freely program. In addition, this product specifically utilizes Infineon‘s Motor Control Engine (MCE) technology. By adopting a turnkey solution based on MCE technology, combined with MCEwizard and MCEdesigner as auxiliary tools, a variable speed drive solution can be easily implemented.
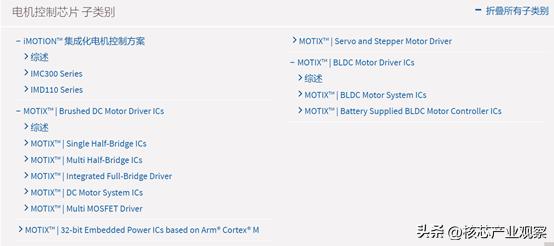
For example, Infineon‘s intelligent integrated half bridge series launched this year: the all-new MOTIX ™ BTN99xx (NovalithIC ™ ), In addition to a P-channel high side and an N-channel low side MOSFET, the BTN99xx also includes an intelligent driver IC fully integrated in a single package, which features ease of use, advanced protection, and scalability, making it suitable for various automotive applications. In addition, BTN99xx also integrates various functions in a single rugged package, making it suitable for applications that require reduced PCB consumption. With its strong reliability, the BTN99xx is also very suitable for other applications such as seat control, electric tailgate and sliding door, fuel pump, etc.
This new device adopts Infineon‘s chip by chip and stacking process, integrated into a sturdy package. Thanks to Infineon‘s latest MOSFET technology and innovative chip thinning process, the normal path resistance of BTN99xx can be significantly reduced by 47% to 5.30 m Ω at 25 ° C, and its current limit can be increased to 75 A. Therefore, BTN99xx is very suitable for miniaturized high current PWM (pulse width modulation) motor drivers.
In fact, MOTIX BTN99xx falls between discrete gate drivers and highly integrated embedded power motor control products based on Arm processors. The BTN99xx series of chips includes two models, BTN9970LV and BTN9990LV, both of which are packaged in a 7 × 8mm HSOF-7 package.
epilogue
From the current chip solutions launched by chip companies, it can be seen that motor drive chips are developing towards a simpler and more user-friendly direction.
Disclaimer: This article is transferred from other platforms and does not represent the views and positions of this site. If there is any infringement or objection, please contact us to delete it. thank you! |